(NaturalNews) A new industrial revolution is brewing.
Industrial 3D printing is making its way from the mainstream to the lab, enabling researchers to obtain parts for scientific instruments in an unprecedented way.
3D printing is already changing how various objects, including tools and clothing, are made. It is part of a process known as additive manufacturing, which creates an object by adding material layer by layer. Additive manufacturing allows scientists to create complex parts for scientific instruments at a fraction of the cost of conventional means.
"Instead of waiting for parts to be ordered and shipped, it's often easier and faster to just build the parts yourself in 3D software, then print those parts on a 3D printer," said
Mike Adams, the Health Ranger, who runs his own forensic food lab.
When Adams needed a part to plug an oil drain on a vacuum pump for an Agilent 7700x ICP-MS instrument, he designed one and printed it out as seen in the pic below. Adams emphasizes that science labs across America need to start using 3D printers more to solve their problems.
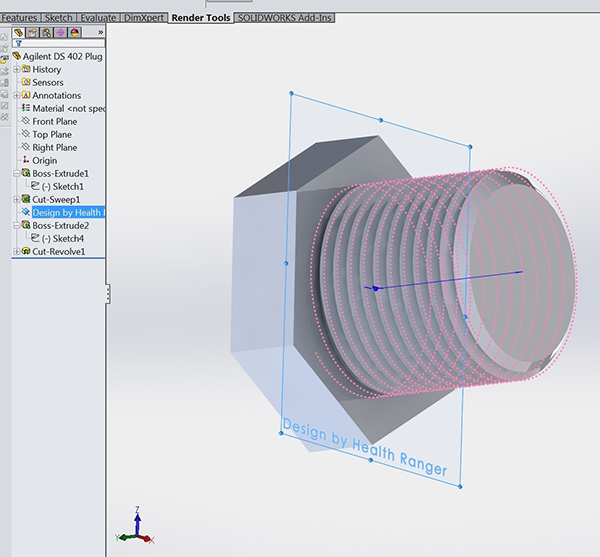
How 3D printing works
The first step in 3D printing is to create a blueprint of the object you want to print. This is achieved using modeling software. Once a design is chosen, it can be sent to the printer. Plastic strands, known as filament, are usually on a spool attached to the printer. The filament is pulled through a tube, liquefied and deposited on a plate to cool. Adams co-developed a polymer filament called "T-glase polar white" to print his plug.
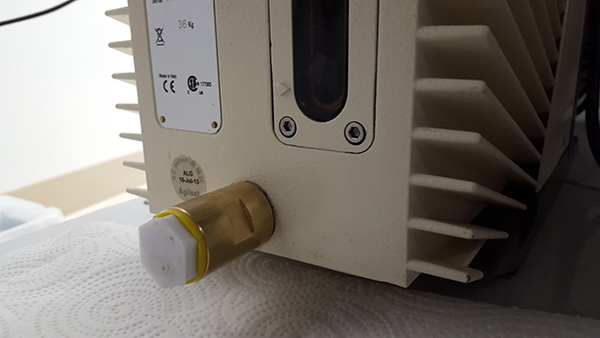
The 3D object is sculpted through layering. The printer lays down one layer of the object at a time until the structure is completely formed. When people first encounter a 3D printer, they ponder all the tailor-made products that could be made from it. Scientists have the same mentality. The only difference is that scientists tend to rely on equipment that is both expensive and highly specialized. In other words, 3D printing has the potential to change the way scientists do science.
Redefining how science is done
The price of 3D printers and filament will likely drop as they become manufactured on a larger scale. As researchers start to share designs from their laboratory hardware, other researchers can use and improve those designs. This will make scientific instruments affordable, not just for academics, but for public schools and citizen scientists conducting independent research.
For ages, scientists had to purchase expensive tools and pay outrageously exorbitant fees if they wanted to do cutting edge research. This isn't the case in the wake of 3D
printers, however. The technology will enable researchers to produce products in the comfort of a lab, sidestepping the stock, shipping and waste attached to other instruments.
Less money and more research time is just half of what
3D printers have to offer. The foremost benefit of 3D printers is their ability to produce tailor-made parts for scientific instruments. Rather than relying on what is commercially available, scientists can print out custom parts for scientific tools. This is particularly useful for scientists conducting cutting edge research, who need highly specialized instruments to make real scientific breakthroughs. In the meantime, universities across the country are wasting millions of dollars on repairing outdated scientific equipment.
In the long term, 3D printing will revolutionize science by blending scientific consumption with scientific production.
Sources include:
TechCrunch.comElsevier.comGigaom.comHBR.orgScience.NaturalNews.com
Receive Our Free Email Newsletter
Get independent news alerts on natural cures, food lab tests, cannabis medicine, science, robotics, drones, privacy and more.
Take Action: Support Natural News by linking to this article from your website
Permalink to this article:
Embed article link: (copy HTML code below):
Reprinting this article:
Non-commercial use OK, cite NaturalNews.com with clickable link.
Follow Natural News on Facebook, Twitter, Google Plus, and Pinterest