(NaturalNews) Over the last several weeks, I put the Ultimaker 2 3D printer through the paces at my 3D print farm in Texas which is producing parts for the
Food Rising project. The printer has been churning out a lot of the parts we're shipping with our Food Rising Mini-Farm Grow System donations, but out of the three Ultimaker 2 printers I've been running,
two are now out of service due to maintenance issues.
There are primarily two problems I've identified with the Ultimaker 2, both of them "show stoppers" in my opinion.
The first is that the filament feed mechanism, which works brilliantly at first, but begins to "slip and click" after a few hundred hours of printing (t-glase). This slipping of the filament feeder appears to be impossible to readily fix: I've tightened and loosened the feel wheel tension, I've disassembled the feed mechanism and cleaned it out, and I've even swapped a "good" feed mechanism from one printer to another, to see if that would make any difference.
It didn't. This feed problem is apparently somewhat widespread:
"The clicking is due to the extruder skipping steps when it can't push the filament hard enough. Several people have had this problem - there are several recent threads about it on the forum," says the
Ultimaker forum. That same message explains that this feed wheel skip is caused by a demand for too high a volume flow rate through the nozzle. However, this explanation is simply not true in my case: I have an enormous nozzle (no jokes, please) running at 0.7mm diameter, which allows THREE TIMES the flow rate of a 0.4mm nozzle (do your math if you fail to understand why, this is middle school mathematics for the area of a circle).
I've even tried slowing the printing speed to 50% to no avail. The "slip and click" continues.
But that's only the first problem with the Ultimaker 2...
Did you break the temperature sensor? Me too...
One of the most frequent maintenance functions you'll perform on any printer is swapping out the print nozzle.
There are lots of reasons you'll need to do this, but one of the most common is the need to drill out the nozzle to a larger size. Many nozzles ship at 0.4mm diameter, but when you're printing functional parts that need high rigidity, you'll need to enlarge those nozzles to at least 0.5mm in diameter (or even larger).
To do this, you usually need to remove the nozzle, drill it out, then replace it. On the Lulzbot Mini or the Type A Machines 3D printer, this is a very simple manner. It's also relatively simple on FlashForge printers or most RepRap-style open source 3D printers.
But on the Ultimaker, the process is almost impossible to carry out without damaging expensive components of the printer.
Specifically, the nozzle is integrated into the hot block, and the hot block has two components jammed into it that are almost impossible to remove without causing damage: the heating element and the PT100 temperature sensor.
Here's a photo of a disassembled Ultimaker 2 hot end and nozzle. You have to do all this and more just to replace the nozzle:
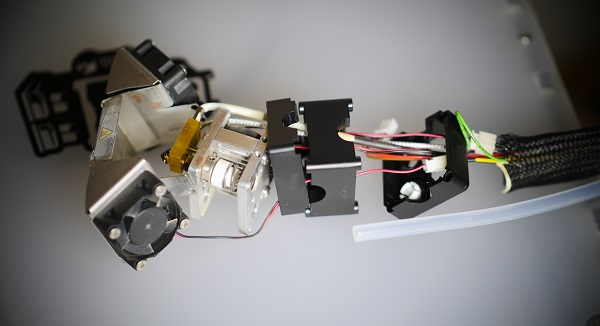
The PT100 temperature sensor is attached with small, delicate wires, yet I found it impossible to remove without damaging it beyond repair. This problem seems quite common with the Ultimaker 2, as you'll find on discussion forums.
If you damage the PT100 temperature sensor, you might have to wait a month to get a replacement. It's not cheap, either.
Printme3D.com sells this sensor for $77.40 all by itself.
While you're waiting for this part to arrive, your $1700 3D printer is a very expensive paper weight. And if you had bought a Lulzbot Mini instead, you could have swapped out the nozzle in about two minutes using a $5 generic nozzle you can buy on Amazon.com.
If you ever have to replace the entire print end, you have to open the bottom panel to access the circuit board which looks like this:
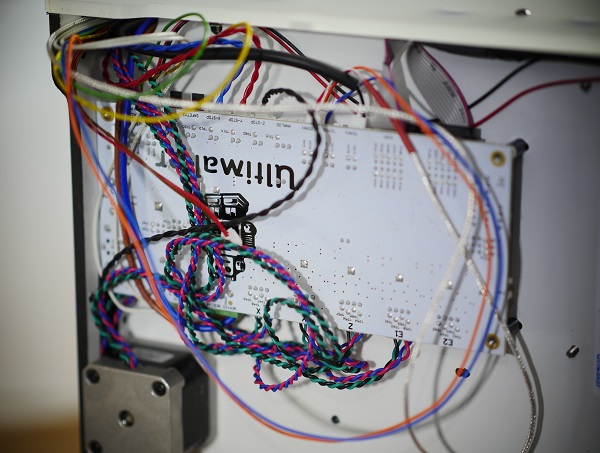
From here, you have to unplug lots of wire connections, including one that's on the inside the circuit board, requiring you to detach the board from the bottom of the printer. One look at this circuit board arrangement makes it clear that user maintenance was not well thought-out:
Unfortunate design decisions neglected to consider maintenance modularity
This problem can only be traced back to
poor design decisions on the part of the Ultimaker manufacturer. Somewhere along the line, somebody made a decision to ignore the idea of modularity and render the most frequently-changed part of this 3D printer (the nozzle) non-serviceable by an ordinary user. In my view, this is a fatal mistake for the simple reason that it leads to users like me writing frustrating reviews like this. I'm not at all unfair to 3D printers: I recently
gave the Lulzbot Mini my Editor's Choice Award for its outstanding design, simplicity and reliability, and I have a very positive review coming soon for the Type A Machines Series 1 3D printer.
Unlike with the Type A Machines 3D printer where you can swap out the entire hot end in about two minutes, the long cabling on the Ultimaker 2 turns a temperature sensor swapout into a long, frustrating job that might reasonably take
two hours or more.
Additionally, the rear feed mechanism posed a problem not found in other printers. When you select the "change material" function from the control panel of the printer, it heats up the nozzle and retracts the filament all the way through the feed tubing and out the feed wheel on the rear of the machine.
Or, at least it's supposed to. What actually happens on the printers I own is that they don't quite retract it enough, leaving an inch or two of filament still in the feed tube. So you have to cancel the function and start it again to get another full retraction cycle going, which finally removes the filament.
Once that happens, the printer often gives me an "X-Y sensor error" which requires a power off restart, after which the problem is cleared. From there, you then have to select "change material" again, which heats the nozzle again, and retracts yet again, to get ready to feed new material into the printer. So a function that takes about 10 seconds on a Type A Machines 3D printer ends up taking an unnecessarily long series of steps to accomplish on the Ultimaker 2.
The bottom line on the Ultimaker 2? When they work, they're awesome. When they don't, they're a real nightmare.
Not suitable for print farm operations
In terms of suitability for a 3D print farm, this puts the Ultimaker 2 out of the running, in my view. You can't have a print farm running on printers that suffer from extremely long down time outages and require complex hardware procedures to perform basic maintenance.
The truth is that
3D printing is going mainstream, and that means 3D printers are being increasingly purchased by people with less technical ability than those of us "geeks" who are well experienced at working on circuit boards, using Dremel tools, customizing mechanical systems and so on. A 3D printer that's acceptable to the masses should never require a user to have skills in micro soldering or to own tools such as diamond rotary micro grinding tips for a Dremel.
So my recommendation is to skip the Ultimaker 2. The hot end problem is a fatal one. Perhaps the Ultimaker 3 will resolve this issue and respect the need for modularity in the print nozzle and its accompanying electronics. Specifically, users need the ability to swap out the hot end or print nozzle without damaging the printer so much that it will no longer operate.
For those looking for a reliable, easy-to-use 3D printer that's also affordable, presently the $1350
Lulzbot Mini is the printer to beat. Replacing the print nozzles is ridiculously easy, and the automatic bed leveling capability is a true game-changer in its ability to save you time and frustration on your 3D prints.
Read my full review here.
And in case you're wondering, I have absolutely no financial ties to any 3D printer manufacturer. All these reviews are 100% independent. Furthermore, I harbor no ill will towards the Ultimaker company. If they come out with a game-changing printer that blows the socks off the Lulzbot, I will gladly buy one and review it!
Take Action: Support Natural News by linking to this article from your website
Permalink to this article:
Embed article link: (copy HTML code below):
Reprinting this article:
Non-commercial use OK, cite NaturalNews.com with clickable link.
Follow Natural News on Facebook, Twitter, Google Plus, and Pinterest